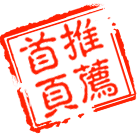
这几天认真学习了政府工作报告,2025年重点工作为振消费、促创新、深改革、稳楼市、惠民生。纵深推进全国统一大市场建设,有效激发各类经营主体活力,开展标准提升引领行动,加强全面质量管理。领导人表述2024年工作中制定修订环保、安全等强制性国家标准。对2025年工作提出了1.开展标准提升引领传统产业优化升级行动。2.完善科技金融、绿色金融、普惠金融、养老金融、数字金融标准体系和基础制度。3.支持内外贸一体化发展,加快解决标准认证、市场渠道等方面问题。4.切实保障外资企业在要素获取、资质许可、标准制定、政府采购等方面的国民待遇。5.适应人民群众高品质居住需要,完善标准规范,推动建设安全、舒适、绿色、智慧的“好房子”。6.完善支持绿色低碳发展的政策和标准体系,营造绿色低碳产业健康发展生态。7.加强义务教育学校标准化建设,推动义务教育优质均衡发展,扩大高中阶段教育学位供给,逐步推行免费学前教育。这是有史以来报告中最多出现标准的。
这里我主要围绕着开展标准提升引领传统产业优化升级行动做进一步展开。党的二十届三中全会提出“健全因地制宜发展新质生产力体制机制”,并强调“以国家标准提升引领传统产业优化升级,支持企业用数智技术、绿色技术改造提升传统产业”。标准化是生产力发展的基石,以标准引领产业发展,是一个国家推动高质量发展、参与高质量竞争的重要标志。标准化建设既凝聚了科技创新成果,又代表了现代产业发展经验,是培育先进生产力不可或缺的纽带,在中国式现代化建设中发挥着引领性作用。标准化建设要与时俱进,引领技术发展方向。生产力决定生产关系,生产关系要与生产力发展相适应。适配的标准体系能够解决生产关系中的质量问题、效率问题、秩序问题、可持续发展问题等。
标准化建设要开放创新,营造良好创新生态。开放性是新质生产力的重要特征,而标准化建设也需要面向世界、坚持开放创新。要营造具有全球竞争力的科技创新生态,助力我国科技创新能力实现从跟跑逐步向并跑、领跑的转变,就必须知道我们的“赛道”“对手”“规则”。当前,面对全球科技创新进入空前密集活跃的时期,类脑智能、量子信息、基因技术、未来网络、深海空天开发、氢能与储能等未来产业,都是最能代表新质生产力的新产业,在这些未来产业的建设过程中,国际上的各项产业技术标准规范都值得我国学习和借鉴,从而设计出符合中国国情的标准体系和实施机制。
去年底工业和信息化部、生态环境部、应急管理部、国家标准化管理委员会联合印发《标准提升引领原材料工业优化升级行动方案(2025—2027年)》(以下简称《行动方案》)。领导人强调,“材料是制造业的基础”“要下大气力推动钢铁、有色、石化、化工、建材等传统产业优化升级”“新材料产业是战略性、基础性产业,也是高科技竞争的关键领域,要奋起直追、迎头赶上”。以标准体系建设为切入口和发力点,发挥标准“指挥棒”作用,引领原材料工业供给高端化、结构合理化、发展绿色化、产业数字化、体系安全化发展,为发展新质生产力,推进新型工业化,加快建设制造强国构筑坚实支撑。以标准“快、优、强”为导向,明确了原材料领域标准化工作的目标任务和重点工程。
工业和信息化部科技司副司长杜广达指出将以先进标准提升引领产业结构优化升级。工业和信息化部将进一步加强先进适用的标准供给,充分发挥标准引领作用。在传统产业领域,将编制钢铁、轻工、机械等行业标准建设指南,加强数智技术、绿色技术等融合领域标准制修订,引领产业优化升级。在新兴产业领域,按照“产品分代、技术分级、研制分期”的思路,加快制定一批先进适用的标准,“产品未动,标准先行”。在未来产业领域,紧跟国内国际技术演进发展趋势,前瞻布局标准化路线图研究。原材料工业是国民经济基础性产业,是制造业高质量发展的重要阵地和坚实保障。将继续牵好标准供给“牛鼻子”,纵深推进标准与产业发展战略、规划、政策联动实施,以先进标准提升引领产业结构优化升级,稳步提升标准国际化水平,不断增强标准在推进产业治理体系和治理能力现代化中的基础性、引领性作用。
在全球产业链重构和技术革命加速的背景下,传统产业优化升级已成为中国经济高质量发展的必由之路。在这一进程中,标准作为产业发展的“技术语言”和“质量标尺”,不仅是技术创新的催化剂,更是产业竞争力的核心支撑。通过开展标准提升行动,以高标准引领传统产业向智能化、绿色化、服务化方向转型,是实现新旧动能转换、重塑产业竞争优势的战略选择。传统产业升级的标准化困境。当前我国传统产业面临“低端锁定”与“标准滞后”的双重挑战。数据显示我国制造业劳动生产率仅为发达国家的1/3至1/4,单位GDP能耗是世界平均水平的1.5倍。在纺织、冶金、机械等传统领域,企业执行的标准中,60%以上仍停留在国际标准的追赶阶段,仅有15%的标准达到国际先进水平。
这种标准化水平的差距直接导致产品附加值低、技术迭代缓慢、国际市场话语权薄弱。以某省装备制造业为例,其80%的中小企业仍采用十年未更新的行业标准,导致产品合格率虽达98%,但高端市场占有率不足5%。这种“高合格率、低竞争力”的悖论,折射出传统标准化体系与市场需求间的结构性矛盾。数据显示,我国传统制造业占规模以上工业增加值的比重仍超过70%,但其数字化渗透率仅为19.2%,单位产值能耗比发达国家高20%-30%。如何通过标准提升这一“隐形引擎”,驱动数智技术与绿色技术深度赋能传统产业,已成为实现新型工业化的关键命题。这场变革不仅是技术升级,更是一场涵盖生产范式、商业模式和产业生态的系统性重塑。
破局之困:传统产业转型的“三重断层”。当前传统产业升级面临标准体系与技术创新、市场需求、全球规则之间的结构性矛盾。1.技术断层:在钢铁、纺织等行业,30%的企业仍在使用十年未更新的工艺标准,导致智能装备应用率不足15%。某陶瓷企业引入工业机器人后,因缺乏设备互联互通标准,系统兼容成本占总投入的40%。2.价值断层:国内机床行业95%以上产品符合国标,但高端市场被德国DIN标准产品占据80%份额,“合规不竞争”现象凸显。3.规则断层:欧盟碳边境调节机制(CBAM)要求进口产品提供全生命周期碳足迹数据,而我国仅有12%的出口企业建立完整碳核算体系,面临每年超500亿元的绿色贸易壁垒。
标准提升的“三重突破路径”。1.技术标准与数字转型的融合创新。在智能工厂建设中,通过制定“数字孪生系统接口标准”“工业大数据质量评估标准”等新型标准,可化解设备互联互通障碍。例如,某家电企业通过实施智能生产线数据采集标准,使设备协同效率提升40%,产品研发周期缩短30%。建议建立“标准-技术-场景”联动机制,在5G+工业互联网、数字供应链等领域率先形成标准群。2.绿色标准牵引全产业链升级。构建覆盖“碳排放核算-清洁生产-循环利用”的全链条标准体系,可破解绿色转型成本难题。浙江绍兴纺织集群通过实施《印染行业绿色工厂评价标准》,推动98家企业完成技术改造,单位产品能耗下降28%,废水回用率提升至75%。未来需加快制定碳足迹追溯、绿电认证等标准,建立与国际互认的绿色标准体系。3.服务标准助推制造服务化转型。在装备制造领域推行《全生命周期服务标准》,可帮助企业从卖产品转向卖服务。三一重工通过制定设备远程运维标准,使服务收入占比从15%提升至35%,利润率提高8个百分点。建议在重点行业建立“产品+服务”标准包,覆盖定制设计、智能运维等新兴业态。
数智赋能:标准牵引的“数字化跃迁”。1.构建智能制造的“数字标准基座”。 设备互联标准:制定《工业设备数据字典通用规范》,解决“万国设备”协议不兼容难题。三一重工通过统一泵车传感器数据标准,使故障诊断效率提升70%。工艺优化标准:在化工领域推行《数字孪生建模指南》,山东某炼厂通过虚拟仿真优化催化裂化参数,能耗降低18%,年增效超2亿元。质量管控标准:开发《AI视觉检测通用技术要求》,广东家电集群应用后,产品缺陷率从0.5%降至0.02%,质量成本下降35%。2.培育产业互联网的“服务标准生态”。制定《制造服务化能力成熟度模型》,推动装备制造企业从卖产品转向卖服务。徐工机械通过制定《工程机械远程运维标准》,实现设备在线监测、预测性维护,服务收入占比突破40%。建立《产业互联网平台接口规范》,浙江“supET”平台连接20万家中小企业,通过标准化数据接口,使供应链协同效率提升50%。
绿色转型:标准驱动的“低碳革命”。1.建立全链条碳治理标准体系。开发《产品碳足迹核算技术通则》,在汽车、建材等行业试点“碳标签”制度。吉利汽车应用碳足迹标准后,单车生产碳排放下降26%,获得欧盟市场绿色通行证。推行《零碳工厂评价规范》,宁德时代宜宾工厂通过建筑光伏一体化、能源管理系统等标准落地,实现100%绿电供应,年减碳62万吨。2.创新循环经济标准范式。制定《再生资源分级利用标准》,河北钢铁集团应用废钢分级标准后,短流程炼钢比例提高至35%,吨钢能耗降低60%。发布《工业园区生态化改造指南》,苏州工业园通过物质流标准化管理,使固废综合利用率达98%,形成年产值超50亿元的循环经济链。
标准生态系统的重构策略。1.构建“金字塔型”标准体系。顶层设计上,应建立“基础通用标准-行业专用标准-企业领跑标准”三级架构。基础层聚焦人工智能、区块链等共性技术;行业层突出细分领域特色;企业层鼓励头部企业制定高于国标的企业标准。青岛海尔牵头制定智慧家庭场景标准,带动产业链500余家企业升级,形成百亿级智能家居生态。2.创新“标准+”政策工具箱。实施“标准领航”工程,对主导制定国际标准的企业给予研发费用加计扣除比例提升至150%的激励;建立标准创新券制度,支持中小企业参与标准研制;在政府采购中设置“标准先进性”评分权重,形成市场倒逼机制。3.打造国际标准合作网络。深度参与ISO、IEC等国际标准组织,在新能源、数字经济等优势领域主导标准制定。中车集团主导制定《高速动车组全寿命周期服务》国际标准,为中国高铁“走出去”增加话语权。建议建立“一带一路”标准协同中心,推动中国标准与沿线国家互认。
协同创新:构建“标准-技术-产业”共生生态。1.打造“金字塔型”标准体系。基础层:研制《工业互联网标识解析体系标准》,建立跨行业数据流通基础设施。行业层:在纺织、机械等22个重点行业制定《数字化转型标准路线图》。企业层:实施“企业标准领跑者”计划,对主导国际标准制定的企业给予研发费用200%加计扣除。2.建设“政产学研用”协同平台。成立国家工业标准创新中心,设立数字与绿色标准专项基金。海尔卡奥斯平台联合12家科研机构,发布全球首个《大规模定制标准体系》,赋能15个行业4.3万家企业转型。建立“标准国际化促进联盟”,推动中国绿色标准与ISO、IEC对接。中国主导制定的《智慧城市基础设施数据交换》国际标准,已在新加坡、沙特等项目落地。
实践启示:从“标准跟随”到“标准引领”。案例1:宁波服装产业数字化升级。通过制定《智能服装工厂建设规范》《个性化定制服务标准》,雅戈尔集团建成全球首个5G西服智能工厂,实现7天定制交付,生产成本降低35%,带动区域200家配套企业完成数字化改造。案例2:内蒙古稀土产业绿色转型。依托《稀土冶炼废水近零排放标准》《磁性材料碳足迹核算标准》,包头稀土高新区建成绿色制造体系,万元产值能耗下降42%,高端磁材市场占有率从15%提升至30%。案例3:宁波注塑机产业集群的标准化升级具有借鉴意义:通过制定《伺服节能注塑机能效分级标准》,淘汰落后产能30%,行业平均能耗下降45%;联合科研机构制定《智能注塑机通信协议标准》,使设备联网率从20%跃升至85%,催生共享工厂等新模式。这种“标准提升-技术突破-模式创新”的良性循环,为传统产业集群升级提供了可复制的路径。
未来图景:标准经济时代的中国方案。随着工业互联网标识解析体系、产品碳足迹数据库等新型标准基础设施全面建成,传统产业将呈现三大趋势:1.制造即服务:基于标准化数据接口,80%的装备制造企业将提供全生命周期服务。2.低碳即竞争力:覆盖300个行业的绿色标准体系,使中国制造碳强度比2020年下降35%。3.标准即规则:在数字经济、新能源等领域主导100项国际标准,形成“中国标准出海”新范式。随着第四次工业革命深入发展,标准正从“技术跟随者”变为“创新引领者”。预计到2030年,全球产业竞争将进入“标准主权”时代,标准制定权将成为国家战略竞争力的核心要素。我国需把握窗口期,在半导体、生物制造等战略领域提前布局标准专利池,培育百家国际标准领军企业,形成标准驱动创新的新型工业化范式。
标准提升行动不是简单的技术规范更新,而是一场重塑产业基因的深刻变革。通过构建具有前瞻性、包容性、开放性的新型标准体系,传统产业将突破低端锁定,在数字化转型与可持续发展中开辟新赛道。这需要政府、企业、科研机构形成协同创新的标准生态,让中国标准成为全球产业升级的“通用货币”。在这场以标准为支点的产业革命中,数智化与绿色化不是二选一的单选题,而是传统产业破茧重生的双翼。通过构建“技术研发-标准制定-产业应用”的闭环生态,中国企业不仅能够突破“低端锁定”困境,更有可能在智能制造、碳中和等新赛道重塑全球产业规则。当标准从“幕后”走向“台前”,中国制造向中国创造的跨越将获得最坚实的技术底座与制度支撑。